ప్లాస్టిక్ భాగాలను ఎలా డిజైన్ చేయాలి
చిన్న వివరణ:
కు ప్లాస్టిక్ భాగాలను రూపొందించండిఉత్పత్తిలో భాగాలు పోషించే పాత్ర మరియు ప్లాస్టిక్ కోసం అచ్చు ప్రక్రియ యొక్క నియమం ఆధారంగా భాగాల ఆకారం, పరిమాణం మరియు ఖచ్చితత్వాన్ని నిర్వచించడం. చివరి ఉత్పత్తి అచ్చు మరియు ప్లాస్టిక్ భాగం తయారీకి డ్రాయింగ్లు.
ఉత్పత్తి తయారీ రూపకల్పనతో మొదలవుతుంది. ప్లాస్టిక్ భాగాల రూపకల్పన ఉత్పత్తి యొక్క అంతర్గత నిర్మాణం, ఖర్చు మరియు పనితీరు యొక్క సాక్షాత్కారాన్ని నేరుగా నిర్ణయిస్తుంది మరియు అచ్చు ఉత్పత్తి, ఖర్చు మరియు చక్రం యొక్క తదుపరి దశను, అలాగే ఇంజెక్షన్ అచ్చు మరియు పోస్ట్-ప్రాసెసింగ్ ప్రక్రియ మరియు వ్యయాన్ని కూడా నిర్ణయిస్తుంది.
ఆధునిక సమాజంలో వివిధ ఉత్పత్తులు, సౌకర్యాలు మరియు ప్రజల జీవితాలలో ప్లాస్టిక్ భాగాలు విస్తృతంగా ఉపయోగించబడుతున్నాయి. ప్లాస్టిక్ భాగాలకు వేర్వేరు ఆకారాలు మరియు విధులు అవసరం. వారు ప్లాస్టిక్ పదార్థాలను ఉపయోగిస్తారు మరియు వాటి లక్షణాలు వైవిధ్యంగా ఉంటాయి. అదే సమయంలో, పరిశ్రమలో ప్లాస్టిక్ భాగాలను తయారు చేయడానికి అనేక మార్గాలు ఉన్నాయి. కాబట్టి ప్లాస్టిక్ భాగాలను రూపొందించడం సాధారణ పని కాదు.
వేర్వేరు భాగం రూపకల్పన మరియు పదార్థం వేర్వేరు ప్రాసెసింగ్ను ఉత్పత్తి చేస్తాయి. అచ్చు ప్లాస్టిక్ కోసం ప్రాసెసింగ్ ప్రధానంగా క్రింద ఉంటుంది:
1.ఇంజక్షన్ అచ్చు
2. బ్లోయింగ్ అచ్చు
3.కంప్రెషన్ అచ్చు
4.రోషనల్ మోల్డింగ్
5.థర్మోఫార్మింగ్
6.ఎక్స్ట్రషన్
7. ఫ్యాబ్రికేషన్
8. ఫోమింగ్
వాటిని భారీగా ఉత్పత్తి చేయడానికి అనేక మార్గాలు ఉన్నాయి. ఇంజెక్షన్ అచ్చు అనేది ప్రసిద్ధ ఉత్పాదక పద్ధతి, ఎందుకంటే ఇంజెక్షన్ అచ్చు 50% ~ 60% ప్లాస్టిక్ భాగాలు బైబ్ ఇంజెక్షన్ అచ్చును ఉత్పత్తి చేస్తాయి, ఇది అధిక-వేగ ఉత్పత్తి సామర్ధ్యం.
మేము రూపొందించిన కొన్ని ప్లాస్టిక్ భాగాల కోసం కేసు చూపించు:
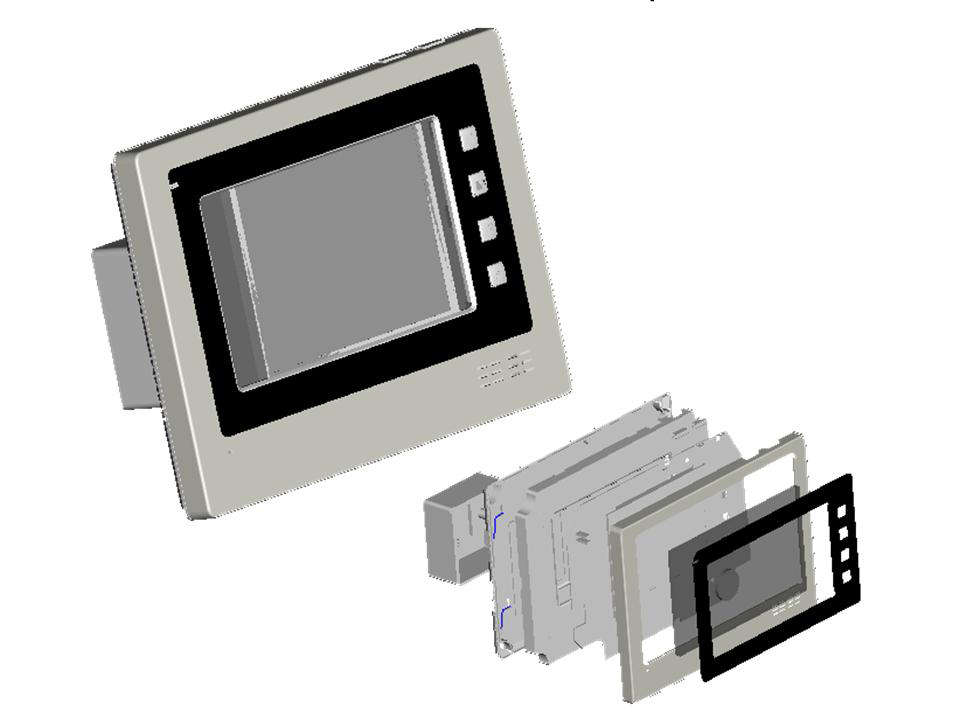
దృష్టి ఫోన్ యొక్క ప్లాస్టిక్ ఎన్క్లోజర్
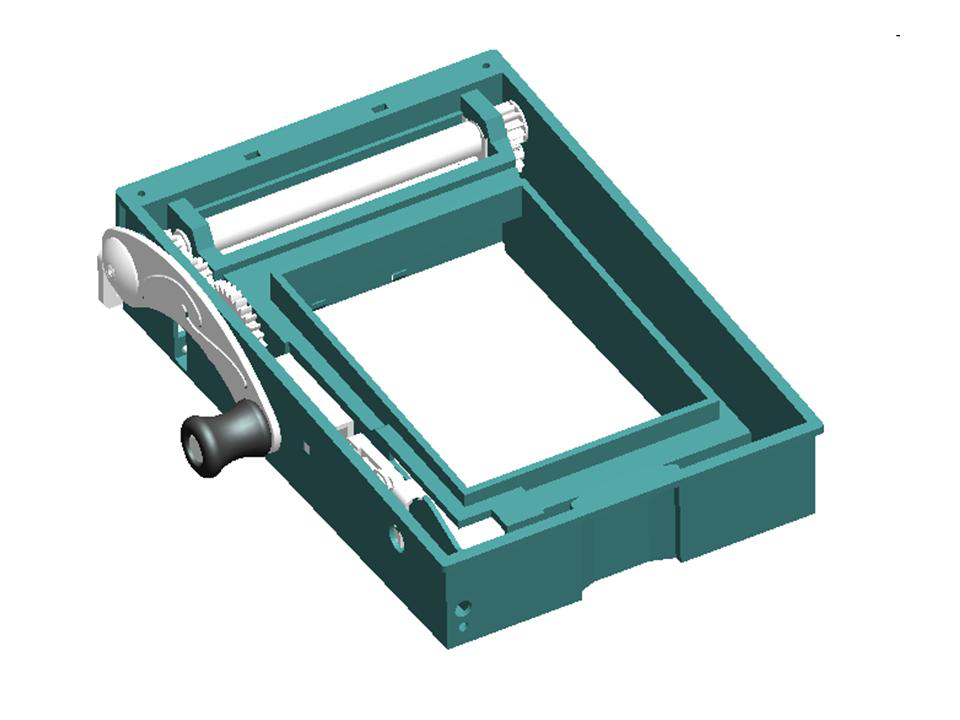
యంత్రాంగం యొక్క ప్లాస్టిక్ భాగాలు
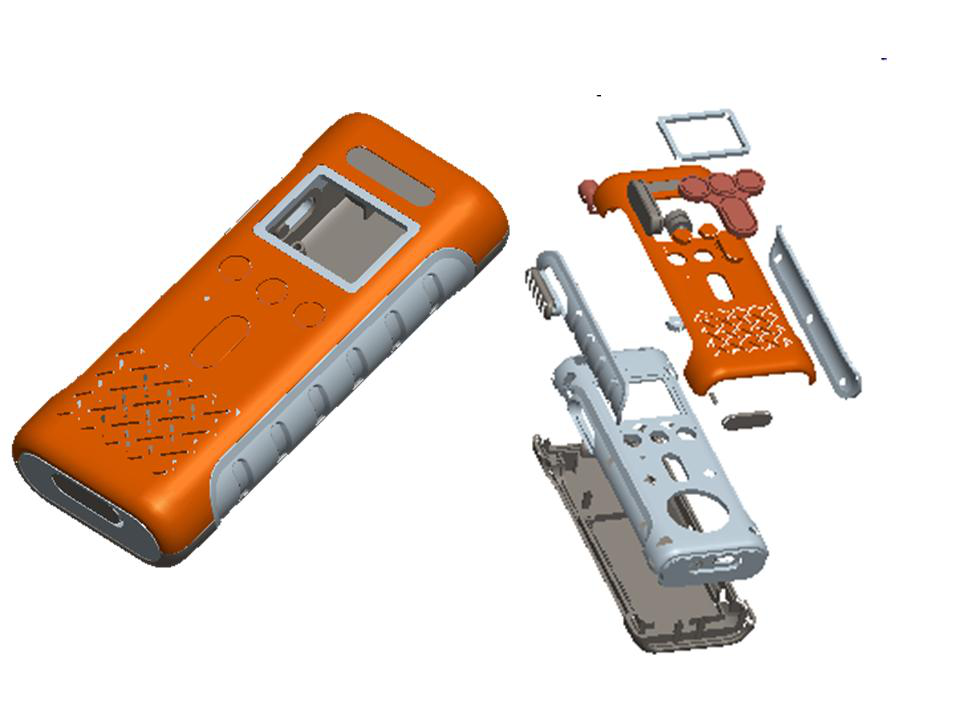
ఎలక్ట్రానిక్ యొక్క ప్లాస్టిక్ కేసులు
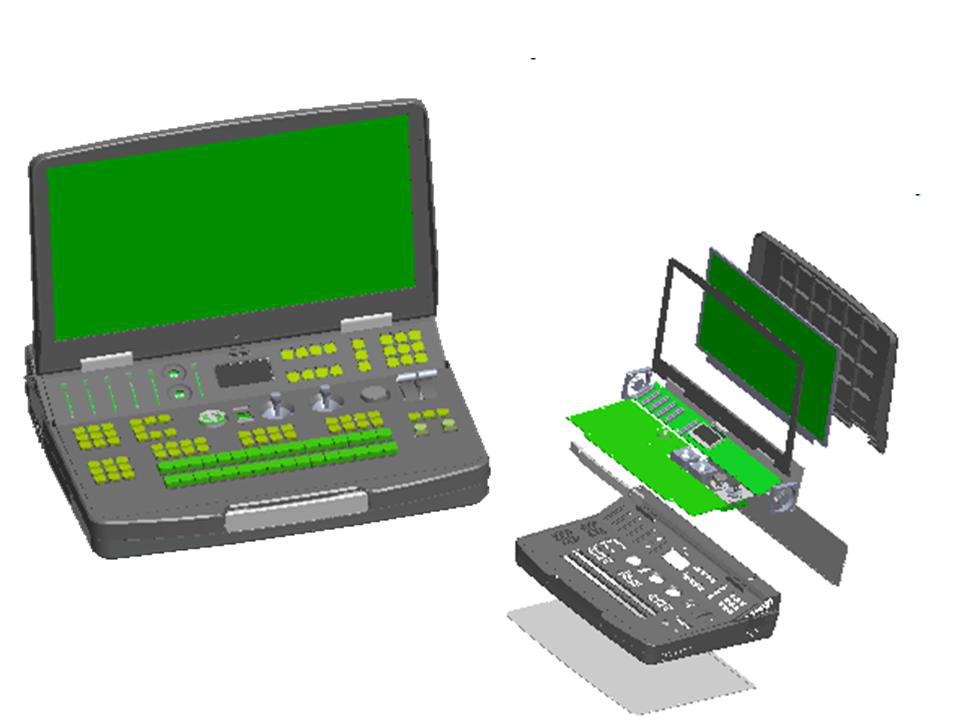
పరికరం కోసం ప్లాస్టిక్ హౌసింగ్
మూడు అంశాలలో ప్లాస్టిక్ భాగాలను ఎలా రూపొందించాలో మేము క్రింద వివరంగా పంచుకుంటాము
* మీరు తెలుసుకోవలసిన ప్లాస్టిక్ భాగాల రూపకల్పన కోసం 10 చిట్కాలు
1. ఉత్పత్తి రూపకల్పన మరియు ఉత్పత్తి యొక్క పరిమాణాన్ని నిర్ణయించండి.
మొత్తం రూపకల్పన ప్రక్రియలో ఇది మొదటి దశ. మార్కెట్ పరిశోధన మరియు కస్టమర్ అవసరాల ప్రకారం, ఉత్పత్తుల రూపాన్ని మరియు పనితీరును నిర్ణయించండి మరియు ఉత్పత్తి అభివృద్ధి పనులను రూపొందించండి.
అభివృద్ధి పని ప్రకారం, అభివృద్ధి బృందం ఉత్పత్తికి సాంకేతిక మరియు సాంకేతిక సాధ్యాసాధ్య విశ్లేషణను నిర్వహిస్తుంది మరియు ఉత్పత్తి యొక్క 3D ప్రదర్శన నమూనాను నిర్మిస్తుంది. అప్పుడు, ఫంక్షన్ రియలైజేషన్ మరియు ప్రొడక్ట్ అసెంబ్లీ ప్రకారం, సాధ్యం భాగాలు ప్రణాళిక చేయబడతాయి.
ఉత్పత్తి డ్రాయింగ్ల నుండి వ్యక్తిగత భాగాలను వేరు చేయండి, ప్లాస్టిక్ భాగాల కోసం ప్లాస్టిక్ రెసిన్ రకాన్ని ఎంచుకోండి
మునుపటి దశలో పొందిన 3 డి మోడల్ నుండి భాగాలను వేరు చేసి వాటిని వ్యక్తిగతంగా రూపొందించడం ఈ దశ. భాగాల యొక్క క్రియాత్మక అవసరాల ప్రకారం, తగిన ప్లాస్టిక్ ముడి పదార్థాలు లేదా హార్డ్వేర్ పదార్థాలను ఎంచుకోండి. ఉదాహరణకు, ABS సాధారణంగా ఉపయోగించబడుతుంది
షెల్, ఎబిఎస్ / బిసి లేదా పిసికి కొన్ని యాంత్రిక లక్షణాలు, లాంప్షేడ్, లాంప్ పోస్ట్ పిఎంఎంఎ లేదా పిసి, గేర్ లేదా వేర్ పార్ట్స్ పిఒఎం లేదా నైలాన్ వంటి పారదర్శక భాగాలు ఉండాలి.
భాగాల యొక్క పదార్థాన్ని ఎంచుకున్న తరువాత, వివరాల రూపకల్పనను ప్రారంభించవచ్చు.
3. డ్రాఫ్ట్ కోణాలను నిర్వచించండి
డ్రాఫ్ట్ కోణాలు అచ్చు నుండి ప్లాస్టిక్ను తొలగించడానికి అనుమతిస్తాయి. చిత్తుప్రతి కోణాలు లేకుండా, తొలగింపు సమయంలో ఘర్షణ కారణంగా ఈ భాగం గణనీయమైన ప్రతిఘటనను అందిస్తుంది. డ్రాఫ్ట్ కోణాలు భాగం లోపల మరియు వెలుపల ఉండాలి. లోతైన భాగం, పెద్ద డ్రాఫ్ట్ కోణం. అంగుళానికి 1 డిగ్రీ డ్రాఫ్ట్ కోణం కలిగి ఉండటం సాధారణ నియమం. తగినంత డ్రాఫ్ట్ కోణం లేకపోవడం వలన భాగం మరియు / లేదా పెద్ద ఎజెక్టర్ పిన్ మార్కుల వైపులా స్క్రాప్లు ఏర్పడవచ్చు (దీని తరువాత మరింత).
బయటి ఉపరితలం యొక్క చిత్తుప్రతి కోణాలు: లోతైన భాగం, పెద్ద చిత్తుప్రతి కోణం. అంగుళానికి 1 డిగ్రీ డ్రాఫ్ట్ కోణం కలిగి ఉండటం సాధారణ నియమం. తగినంత డ్రాఫ్ట్ కోణం లేకపోవడం వలన భాగం మరియు / లేదా పెద్ద ఎజెక్టర్ పిన్ మార్కుల వైపులా స్క్రాప్లు ఏర్పడవచ్చు (దీని తరువాత మరింత).
సాధారణంగా, మంచి రూపాన్ని కలిగి ఉండటానికి, భాగాల ఉపరితలంపై ఆకృతి తయారవుతుంది. ఆకృతితో ఉన్న గోడ కఠినమైనది, ఘర్షణ పెద్దది, మరియు దానిని కుహరం నుండి తొలగించడం అంత సులభం కాదు, కాబట్టి దీనికి పెద్ద డ్రాయింగ్ కోణం అవసరం. ముతక ఆకృతి, పెద్ద ముసాయిదా కోణం అవసరం.
గోడ మందం / ఏకరీతి మందం నిర్వచించండి
కింది కారణాల వల్ల ఇంజెక్షన్ అచ్చులో ఘన ఆకారం అచ్చు అక్కరలేదు:
1). కూలింగ్ సమయం గోడ మందం యొక్క చదరపుకి అనులోమానుపాతంలో ఉంటుంది. ఘన కోసం దీర్ఘ శీతలీకరణ సమయం భారీ ఉత్పత్తి యొక్క ఆర్థిక వ్యవస్థను ఓడిస్తుంది. (వేడి యొక్క కండక్టర్)
2) .టిక్కర్ విభాగం సన్నగా ఉండే విభాగం కంటే కుదించబడుతుంది, తద్వారా వార్పేజ్ లేదా సింక్ మార్క్ మొదలైన అవకలన సంకోచాన్ని పరిచయం చేస్తుంది (ప్లాస్టిక్స్ మరియు పివిటి లక్షణాల సంకోచ లక్షణాలు)
అందువల్ల ప్లాస్టిక్ పార్ట్ డిజైన్ కోసం మాకు ప్రాథమిక నియమం ఉంది; సాధ్యమైనంతవరకు గోడ మందం భాగం అంతటా ఏకరీతిగా లేదా స్థిరంగా ఉండాలి. ఈ గోడ మందాన్ని నామమాత్రపు గోడ మందం అంటారు.
భాగంలో ఏదైనా ఘన విభాగం ఉంటే, కోర్ని ప్రవేశపెట్టడం ద్వారా దానిని బోలుగా చేయాలి. ఇది కోర్ చుట్టూ ఏకరీతి గోడ మందాన్ని నిర్ధారించాలి.
3). గోడ మందాన్ని నిర్ణయించడానికి పరిగణనలు ఏమిటి?
ఇది మందంగా ఉండాలి మరియు ఉద్యోగానికి తగినంత గట్టిగా ఉండాలి. గోడ మందం 0.5 నుండి 5 మిమీ కావచ్చు.
ఇది వేగంగా చల్లబరచడానికి తగినంత సన్నగా ఉండాలి, ఫలితంగా తక్కువ భాగం బరువు మరియు అధిక ఉత్పాదకత ఉంటుంది.
గోడ మందంలో ఏదైనా వైవిధ్యం సాధ్యమైనంత కనిష్టంగా ఉంచాలి.
విభిన్న గోడ మందంతో ప్లాస్టిక్ భాగం విభిన్న శీతలీకరణ రేట్లు మరియు విభిన్న సంకోచాలను అనుభవిస్తుంది. అటువంటి సందర్భంలో దగ్గరి సహనాన్ని సాధించడం చాలా కష్టం మరియు చాలా సార్లు అసాధ్యం అవుతుంది. గోడ మందం వైవిధ్యం తప్పనిసరి అయినప్పుడు, రెండింటి మధ్య పరివర్తన క్రమంగా ఉండాలి.
5. భాగాల మధ్య కనెక్షన్ డిజైన్
సాధారణంగా మనం రెండు షెల్స్ను కలిపి కనెక్ట్ చేయాలి. అంతర్గత భాగాలను (పిసిబి అసెంబ్లీ లేదా మెకానిజం) ఉంచడానికి వాటి మధ్య పరివేష్టిత గదిని ఏర్పాటు చేయడం.
కనెక్షన్ యొక్క సాధారణ రకాలు:
1). స్నాప్ హుక్స్:
స్నాప్ హుక్స్ కనెక్షన్ సాధారణంగా చిన్న మరియు మధ్య తరహా ఉత్పత్తులలో ఉపయోగించబడుతుంది. దీని లక్షణం ఏమిటంటే స్నాప్ హుక్స్ సాధారణంగా భాగాల అంచు వద్ద అమర్చబడి ఉంటాయి మరియు ఉత్పత్తి పరిమాణాన్ని చిన్నగా చేయవచ్చు. సమావేశమైనప్పుడు, స్క్రూడ్రైవర్, అల్ట్రాసోనిక్ వెల్డింగ్ డై మరియు ఇతరులు వంటి సాధనాలను ఉపయోగించకుండా నేరుగా మూసివేయబడుతుంది. ప్రతికూలత ఏమిటంటే స్నాప్ హుక్స్ అచ్చును మరింత క్లిష్టంగా కలిగిస్తుంది. స్నాప్ హుక్స్ కనెక్షన్ను గ్రహించడానికి మరియు అచ్చు వ్యయాన్ని పెంచడానికి స్లైడర్ మెకానిజం మరియు లిఫ్టర్ మెకానిజం అవసరం.
2). స్క్రూ కీళ్ళు:
స్క్రూ కీళ్ళు దృ firm మైన మరియు నమ్మదగినవి. ముఖ్యంగా, స్క్రూ + గింజ స్థిరీకరణ చాలా నమ్మదగినది మరియు మన్నికైనది, ఇది పగుళ్లు లేకుండా బహుళ విడదీయడానికి అనుమతిస్తుంది. పెద్ద లాకింగ్ శక్తి మరియు బహుళ తొలగింపు కలిగిన ఉత్పత్తులకు స్క్రూ కనెక్షన్ అనుకూలంగా ఉంటుంది. ప్రతికూలత ఏమిటంటే స్క్రూ కాలమ్ ఎక్కువ స్థలాన్ని తీసుకుంటుంది.
3). మౌంటు ఉన్నతాధికారులు:
ఉన్నతాధికారుల కనెక్షన్ మౌస్ మరియు రంధ్రాల మధ్య గట్టి సమన్వయం ద్వారా రెండు భాగాలను పరిష్కరించడం. ఉత్పత్తులను విడదీయడానికి అనుమతించేంత కనెక్షన్ ఈ మార్గం బలంగా లేదు. ప్రతికూలత ఏమిటంటే, వేరుచేసే సమయం పెరిగే కొద్దీ లాకింగ్ బలం తగ్గుతుంది.
4). అల్ట్రాసోనిక్ వెల్డింగ్:
అల్ట్రాసోనిక్ వెల్డింగ్ అంటే రెండు భాగాలను అల్ట్రాసోనిక్ అచ్చులో ఉంచడం మరియు అల్ట్రాసోనిక్ వెల్డింగ్ యంత్రం యొక్క చర్య కింద కాంటాక్ట్ ఉపరితలాన్ని కలపడం. ఉత్పత్తి పరిమాణం చిన్నదిగా ఉంటుంది, ఇంజెక్షన్ అచ్చు చాలా సులభం, మరియు కనెక్షన్ దృ is ంగా ఉంటుంది. ప్రతికూలత అల్ట్రాసోనిక్ అచ్చు మరియు అల్ట్రాసోనిక్ వెల్డింగ్ యంత్రాన్ని ఉపయోగించడం, ఉత్పత్తి పరిమాణం చాలా పెద్దది కాదు. కూల్చివేసిన తరువాత, అల్ట్రాసోనిక్ భాగాలను మళ్లీ ఉపయోగించలేరు.
6.అండర్కట్స్
అండర్కట్స్ అంటే అచ్చులో సగం తొలగించడంలో అంతరాయం కలిగించే అంశాలు. డిజైన్లో ఎక్కడైనా అండర్కట్స్ కనిపిస్తాయి. డ్రాఫ్ట్ కోణం లేకపోవడం కంటే అధ్వాన్నంగా లేకపోతే ఇవి ఆమోదయోగ్యం కాదు. అయితే, కొన్ని అండర్కట్స్ అవసరం మరియు / లేదా అనివార్యమైనవి. ఆ సందర్భాలలో, అవసరం
అచ్చులోని భాగాలను స్లైడింగ్ / కదిలించడం ద్వారా అండర్కట్స్ ఉత్పత్తి అవుతాయి.
అచ్చును ఉత్పత్తి చేసేటప్పుడు అండర్కట్లను సృష్టించడం చాలా ఖరీదైనదని గుర్తుంచుకోండి మరియు కనిష్టంగా ఉంచాలి.
7. మద్దతు రిబ్స్ / గుస్సెట్స్
ప్లాస్టిక్ భాగంలోని పక్కటెముకలు భాగం యొక్క దృ ff త్వాన్ని (లోడ్ మరియు పార్ట్ విక్షేపం మధ్య సంబంధం) మెరుగుపరుస్తాయి మరియు దృ g త్వాన్ని పెంచుతాయి. పక్కటెముక దిశలో కరిగే ప్రవాహాన్ని వేగవంతం చేస్తున్నందున ఇది అచ్చు-సామర్థ్యాన్ని కూడా పెంచుతుంది.
పక్కటెముకలు గరిష్ట ఒత్తిడి మరియు భాగం యొక్క కనిపించని ఉపరితలాలపై విక్షేపం యొక్క దిశలో ఉంచబడతాయి. అచ్చు నింపడం, కుదించడం మరియు ఎజెక్షన్ కూడా పక్కటెముక నియామక నిర్ణయాలను ప్రభావితం చేయాలి.
నిలువు గోడతో చేరని పక్కటెముకలు ఆకస్మికంగా ముగియకూడదు. నామమాత్రపు గోడకు క్రమంగా మారడం ఒత్తిడి ఏకాగ్రతకు ప్రమాదాన్ని తగ్గించాలి.
పక్కటెముక - కొలతలు
పక్కటెముకలు క్రింది కొలతలు కలిగి ఉండాలి.
సింక్ గుర్తును నివారించడానికి పక్కటెముక మందం నామమాత్రపు గోడ మందం 0.5 నుండి 0.6 రెట్లు ఉండాలి.
పక్కటెముక ఎత్తు నామమాత్రపు గోడ మందం 2.5 నుండి 3 రెట్లు ఉండాలి.
ఎజెక్షన్ను సులభతరం చేయడానికి పక్కటెముక 0.5 నుండి 1.5-డిగ్రీల డ్రాఫ్ట్ యాంగిల్ కలిగి ఉండాలి.
పక్కటెముక బేస్ వ్యాసార్థం 0.25 నుండి 0.4 రెట్లు నామమాత్రపు గోడ మందం కలిగి ఉండాలి.
రెండు పక్కటెముకల మధ్య దూరం 2 నుండి 3 రెట్లు (లేదా అంతకంటే ఎక్కువ) నామమాత్రపు గోడ మందం ఉండాలి.
8. రేడియస్డ్ అంచులు
రెండు ఉపరితలాలు కలిసినప్పుడు, అది ఒక మూలను ఏర్పరుస్తుంది. మూలలో, గోడ మందం నామమాత్రపు గోడ మందం 1.4 రెట్లు పెరుగుతుంది. ఇది అవకలన సంకోచం మరియు అచ్చుపోసిన ఒత్తిడి మరియు ఎక్కువ శీతలీకరణ సమయానికి దారితీస్తుంది. అందువల్ల, సేవలో వైఫల్యం ప్రమాదం పదునైన మూలల్లో పెరుగుతుంది.
ఈ సమస్యను పరిష్కరించడానికి, మూలలను వ్యాసార్థంతో సున్నితంగా చేయాలి. వ్యాసార్థాన్ని బాహ్యంగా అలాగే అంతర్గతంగా అందించాలి. అంతర్గత పదునైన మూలలో ఎప్పుడూ పగుళ్లు ఉండవు. వ్యాసార్థం స్థిరంగా గోడ మందం నియమానికి ధృవీకరించే విధంగా ఉండాలి. మూలల వద్ద 0.6 నుండి 0.75 రెట్లు గోడ మందం వ్యాసార్థం కలిగి ఉండటం మంచిది. అంతర్గత పదునైన మూలలో ఎప్పుడూ పగుళ్లు ఉండవు.
9.స్క్రూ బాస్ డిజైన్
రెండు సగం కేసులను కలిసి పరిష్కరించడానికి మేము ఎల్లప్పుడూ స్క్రూలను ఉపయోగిస్తాము, లేదా పిసిబిఎ లేదా ఇతర భాగాలను ప్లాస్టిక్ భాగాలపై కట్టుకోండి. కాబట్టి స్క్రూ ఉన్నతాధికారులు స్క్రూ మరియు స్థిర భాగాలకు నిర్మాణం.
స్క్రూ బాస్ స్థూపాకార ఆకారంలో ఉంటుంది. యజమాని తల్లి భాగంతో బేస్ వద్ద లింక్ చేయబడవచ్చు లేదా అది ప్రక్కన అనుసంధానించబడి ఉండవచ్చు. వైపు లింక్ చేయడం వల్ల ప్లాస్టిక్ యొక్క మందపాటి విభాగానికి దారితీయవచ్చు, ఇది సింక్ గుర్తుకు కారణమవుతుంది మరియు శీతలీకరణ సమయాన్ని పెంచుతుంది. స్కెచ్లో చూపిన విధంగా బాస్ పక్కటెముక ద్వారా పక్క గోడకు అనుసంధానించడం ద్వారా ఈ సమస్యను పరిష్కరించవచ్చు. బట్టర్ పక్కటెముకలను అందించడం ద్వారా బాస్ కఠినంగా చేయవచ్చు.
మరికొన్ని భాగాలను కట్టుకోవడానికి బాస్ మీద స్క్రూ ఉపయోగించబడుతుంది. థ్రెడ్ ఏర్పాటు రకం మరలు మరియు ట్రెడ్ కట్టింగ్ రకం మరలు ఉన్నాయి. థర్మోప్లాస్టిక్స్పై థ్రెడ్ ఫార్మింగ్ స్క్రూలను ఉపయోగిస్తారు మరియు థ్రెడ్ కటింగ్ స్క్రూలను అస్థిర థర్మోసెట్ ప్లాస్టిక్ భాగాలపై ఉపయోగిస్తారు.
థ్రెడ్ ఫార్మింగ్ స్క్రూలు చల్లని ప్రవాహం ద్వారా బాస్ యొక్క అంతర్గత గోడపై ఆడ థ్రెడ్లను ఉత్పత్తి చేస్తాయి - ప్లాస్టిక్ కట్ కాకుండా స్థానికంగా వైకల్యంతో ఉంటుంది.
స్క్రూ చొప్పించే శక్తులను మరియు సేవలో స్క్రూపై ఉంచిన భారాన్ని తట్టుకోవటానికి స్క్రూ బాస్ సరైన కొలతలు ఉండాలి.
థ్రెడ్ స్ట్రిప్పింగ్ మరియు స్క్రూ పుల్ అవుట్ కు నిరోధకత కోసం స్క్రూకు సంబంధించి బోర్ యొక్క పరిమాణం కీలకం.
బాస్ బయటి వ్యాసం హూప్ ఒత్తిడిని తట్టుకునేంత పెద్దదిగా ఉండాలి.
చిన్న పొడవు కోసం ఎంట్రీ గూడ వద్ద బోర్ కొంచెం పెద్ద వ్యాసం కలిగి ఉంటుంది. డ్రైవింగ్ చేయడానికి ముందు స్క్రూను గుర్తించడంలో ఇది సహాయపడుతుంది. ఇది బాస్ యొక్క ఓపెన్ ఎండ్ వద్ద ఒత్తిడిని కూడా తగ్గిస్తుంది.
పాలిమర్ తయారీదారులు తమ పదార్థాల కోసం బాస్ యొక్క కోణాన్ని నిర్ణయించడానికి మార్గదర్శకాలను ఇస్తారు. స్క్రూ తయారీదారులు స్క్రూ కోసం సరైన బోర్ పరిమాణానికి మార్గదర్శకాలను కూడా ఇస్తారు.
బాస్ లో స్క్రూ బోర్ చుట్టూ బలమైన వెల్డ్ కీళ్ళు ఉండేలా జాగ్రత్త తీసుకోవాలి.
దూకుడు వాతావరణంలో విఫలమయ్యే అవకాశం ఉన్నందున బాస్ లో అచ్చుపోసిన ఒత్తిడిని నివారించడానికి జాగ్రత్త తీసుకోవాలి.
బాస్ లో బోర్ థ్రెడ్ లోతు కంటే లోతుగా ఉండాలి.
10. ఉపరితల అలంకరణ
కొన్నిసార్లు, మంచి రూపాన్ని పొందడానికి, ప్లాస్టిక్ కేసు యొక్క ఉపరితలంపై మేము తరచుగా ప్రత్యేక చికిత్స చేస్తాము.
అవి: ఆకృతి, అధిక నిగనిగలాడే, స్ప్రే పెయింటింగ్, లేజర్ చెక్కడం, వేడి స్టాంపింగ్, ఎలక్ట్రోప్లేటింగ్ మరియు మొదలైనవి. ఉత్పత్తి యొక్క రూపకల్పనలో ముందుగానే పరిగణనలోకి తీసుకోవడం అవసరం, తరువాతి ప్రాసెసింగ్ సాధించలేము లేదా పరిమాణ మార్పులను ఉత్పత్తి అసెంబ్లీని ప్రభావితం చేస్తుంది.